علم الكيمياء
تاريخ الكيمياء والعلماء المشاهير
التحاضير والتجارب الكيميائية
المخاطر والوقاية في الكيمياء
اخرى
مقالات متنوعة في علم الكيمياء
كيمياء عامة
الكيمياء التحليلية
مواضيع عامة في الكيمياء التحليلية
التحليل النوعي والكمي
التحليل الآلي (الطيفي)
طرق الفصل والتنقية
الكيمياء الحياتية
مواضيع عامة في الكيمياء الحياتية
الكاربوهيدرات
الاحماض الامينية والبروتينات
الانزيمات
الدهون
الاحماض النووية
الفيتامينات والمرافقات الانزيمية
الهرمونات
الكيمياء العضوية
مواضيع عامة في الكيمياء العضوية
الهايدروكاربونات
المركبات الوسطية وميكانيكيات التفاعلات العضوية
التشخيص العضوي
تجارب وتفاعلات في الكيمياء العضوية
الكيمياء الفيزيائية
مواضيع عامة في الكيمياء الفيزيائية
الكيمياء الحرارية
حركية التفاعلات الكيميائية
الكيمياء الكهربائية
الكيمياء اللاعضوية
مواضيع عامة في الكيمياء اللاعضوية
الجدول الدوري وخواص العناصر
نظريات التآصر الكيميائي
كيمياء العناصر الانتقالية ومركباتها المعقدة
مواضيع اخرى في الكيمياء
كيمياء النانو
الكيمياء السريرية
الكيمياء الطبية والدوائية
كيمياء الاغذية والنواتج الطبيعية
الكيمياء الجنائية
الكيمياء الصناعية
البترو كيمياويات
الكيمياء الخضراء
كيمياء البيئة
كيمياء البوليمرات
مواضيع عامة في الكيمياء الصناعية
الكيمياء الاشعاعية والنووية
High-Density Polyethylene
المؤلف:
sami matar & Lewis. F. Hatch
المصدر:
Chemistry of PETROCHEMICAL PROCESSES
الجزء والصفحة:
p 327
20-9-2017
1037
High-Density Polyethylene
High-density polyethylene (HDPE) is produced by a low-pressure process in a fluid-bed reactor. Catalysts used for HDPE are either of the Zieglar-type (a complex of Al(C2H5)3 and α-TiCl4) or silicaalumina impregnated with a metal oxide such as chromium oxide or molybdenum oxide. Reaction conditions are generally mild, but they differ from one process to another. In the newer Unipol process (Figure 1.1) used to produce both HDPE and LLDPE, the reaction occurs in the gas phase.
Ethylene and the comonomers (propene, 1-butene, etc.) are fed to the reactor containing a fluidized bed of growing polymer particles. Operation temperature and pressure are approximately 100°C and 20 atmospheres. A single-stage centrifugal compressor circulates unreacted ethylene. The circulated gas fluidizes the bed and removes some of the exothermic reaction heat. The product from the reactor is mixed with additives and then pelletized. New modifications for gas-phase processes have been reviewed by Sinclair.
The polymerization of ethylene can also occur in a liquid-phase system where a hydrocarbon diluent is added. This requires a hydrocarbon recovery system. High-density polyethylene is characterized by a higher crystallinity and higher melting temperature than LDPE due to the absence of branching.
Figure 1.1. The Union Carbide Unipol process for producing HDPE: (1) reactor, (2) single-stage centrifugal compressor, (3) heat exchanger, (4) discharge tank.
Some branching could be incorporated in the backbone of the polymer by adding variable amounts of comonomers such as hexene. These comonomers modify the properties of HDPE for specific applications.
الاكثر قراءة في كيمياء البوليمرات
اخر الاخبار
اخبار العتبة العباسية المقدسة
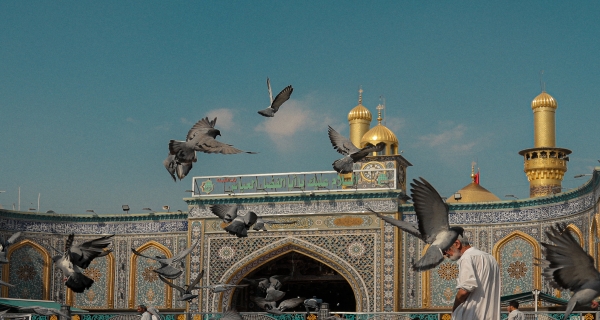
الآخبار الصحية
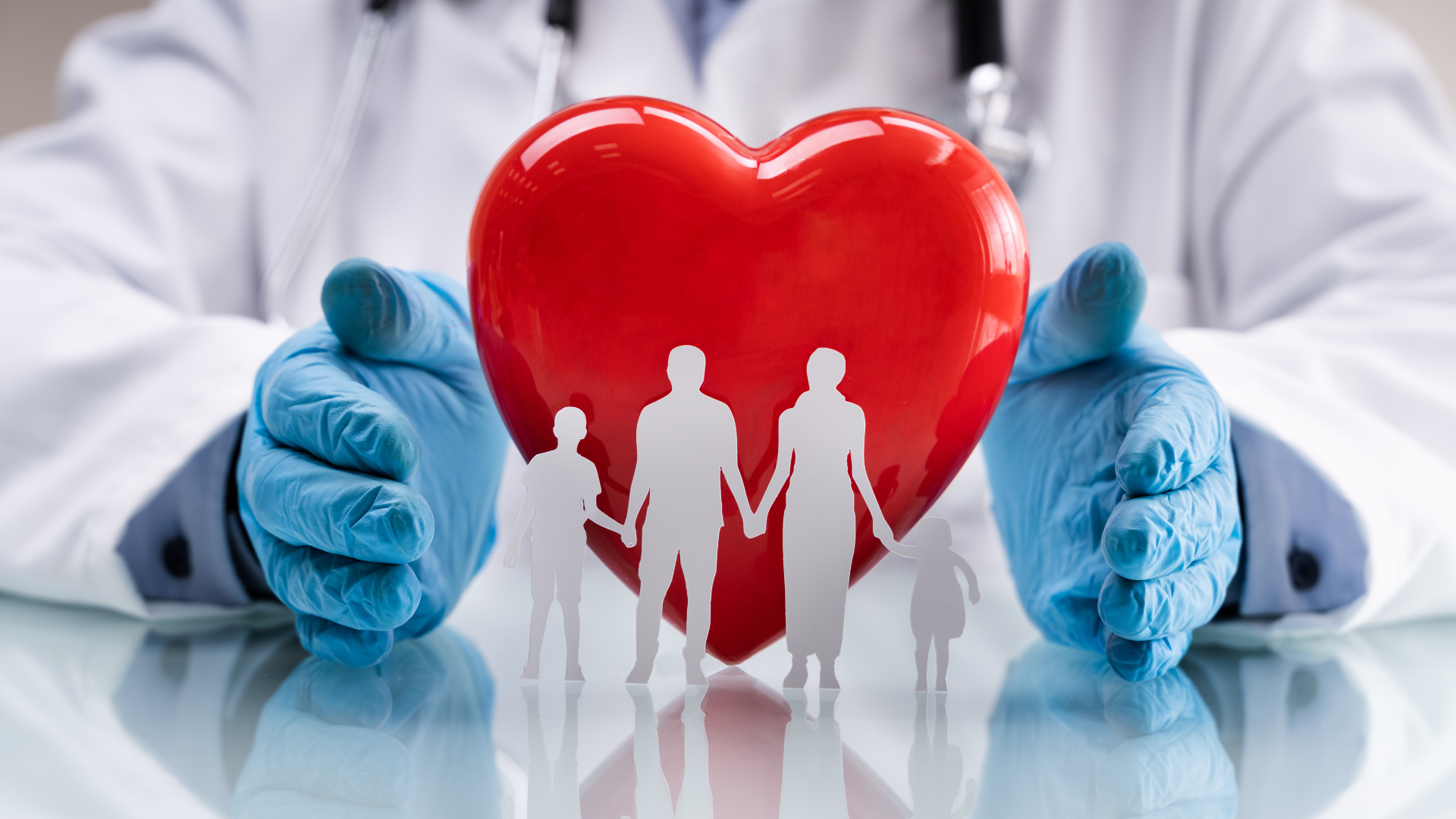