النبات
مواضيع عامة في علم النبات
الجذور - السيقان - الأوراق
النباتات الوعائية واللاوعائية
البذور (مغطاة البذور - عاريات البذور)
الطحالب
النباتات الطبية
الحيوان
مواضيع عامة في علم الحيوان
علم التشريح
التنوع الإحيائي
البايلوجيا الخلوية
الأحياء المجهرية
البكتيريا
الفطريات
الطفيليات
الفايروسات
علم الأمراض
الاورام
الامراض الوراثية
الامراض المناعية
الامراض المدارية
اضطرابات الدورة الدموية
مواضيع عامة في علم الامراض
الحشرات
التقانة الإحيائية
مواضيع عامة في التقانة الإحيائية
التقنية الحيوية المكروبية
التقنية الحيوية والميكروبات
الفعاليات الحيوية
وراثة الاحياء المجهرية
تصنيف الاحياء المجهرية
الاحياء المجهرية في الطبيعة
أيض الاجهاد
التقنية الحيوية والبيئة
التقنية الحيوية والطب
التقنية الحيوية والزراعة
التقنية الحيوية والصناعة
التقنية الحيوية والطاقة
البحار والطحالب الصغيرة
عزل البروتين
هندسة الجينات
التقنية الحياتية النانوية
مفاهيم التقنية الحيوية النانوية
التراكيب النانوية والمجاهر المستخدمة في رؤيتها
تصنيع وتخليق المواد النانوية
تطبيقات التقنية النانوية والحيوية النانوية
الرقائق والمتحسسات الحيوية
المصفوفات المجهرية وحاسوب الدنا
اللقاحات
البيئة والتلوث
علم الأجنة
اعضاء التكاثر وتشكل الاعراس
الاخصاب
التشطر
العصيبة وتشكل الجسيدات
تشكل اللواحق الجنينية
تكون المعيدة وظهور الطبقات الجنينية
مقدمة لعلم الاجنة
الأحياء الجزيئي
مواضيع عامة في الاحياء الجزيئي
علم وظائف الأعضاء
الغدد
مواضيع عامة في الغدد
الغدد الصم و هرموناتها
الجسم تحت السريري
الغدة النخامية
الغدة الكظرية
الغدة التناسلية
الغدة الدرقية والجار الدرقية
الغدة البنكرياسية
الغدة الصنوبرية
مواضيع عامة في علم وظائف الاعضاء
الخلية الحيوانية
الجهاز العصبي
أعضاء الحس
الجهاز العضلي
السوائل الجسمية
الجهاز الدوري والليمف
الجهاز التنفسي
الجهاز الهضمي
الجهاز البولي
المضادات الحيوية
مواضيع عامة في المضادات الحيوية
مضادات البكتيريا
مضادات الفطريات
مضادات الطفيليات
مضادات الفايروسات
علم الخلية
الوراثة
الأحياء العامة
المناعة
التحليلات المرضية
الكيمياء الحيوية
مواضيع متنوعة أخرى
الانزيمات
Freeze drying
المؤلف:
Clive Dennison
المصدر:
A guide to protein isolation
الجزء والصفحة:
17-4-2016
1818
Freeze drying
Freeze drying is a method for the removal of water from a sample kept at low temperature, the water being removed directly from ice into the vapour phase by sublimation. It is a non-specific method as all of the non-volatile solutes are concentrated.
A major use of freeze-drying is for long term storage (preservation) of proteins or other biological samples. By reducing the water content to a very low level, microbial growth is inhibited and spoilage of the stored material is prevented. Aqueous-phase chemical reactions are also inhibited and this helps to preserve the sample. It may be noted that if the water is not removed, a temperature of ca. -70∞C is required in order to stop aqueous-phase reactions, i.e. a deep-freeze at -20C is not cold enough.
Freeze drying may destroy the activity of some enzymes and, if it is important to retain the activity, this should always be checked before freeze-drying is used to preserve a particular protein.
1.1 Theoretical and practical considerations in freeze-drying
Figure 1. Measurement of the vapour pressure of water.
In order to understand how a freeze-dryer works, it is important to understand the concept of vapour pressure. What is “vapour pressure”? Consider the set-up shown in Fig. 1; a sealed container containing only a liquid (water) and its vapour, i.e. with no other gases present, and with a pressure gauge to monitor the (vapour) pressure. In this way, the vapour pressure can be measured as the temperature of the set-up is changed. If this is done, it will be noticed that the measured pressure (the vapour pressure) changes with the temperature as shown in Fig. 2. If there are other gases present then the vapour will contribute a part of the total pressure, i.e. the total pressure will be the vapour pressure at that temperature plus the (partial) pressures of the other gases.
Figure 2. The vapour pressure of water as a function of temperature.
Notice that at 100∞C, the standard boiling point of water, the vapour pressure of water is 760 mm Hg, which is the standard atmospheric pressure. This illustrates the important principle that a liquid will boil when its vapour pressure becomes equal to the environmental atmospheric pressure.
At ca. 0C (at pressures of ambient or below), water undergoes a phase change from a liquid to a solid, ice. The vapour pressure of ice is relatively low (compared to that of water) and is asymptotic to zero as shown in Fig. 3.
Figure 3. The vapour pressure of ice as a function of temperature.
Just as a liquid will boil when its vapour pressure becomes equal to the environmental pressure, so a solid will sublime from the solid state to the vapour state when its vapour pressure becomes equal to the environmental atmospheric pressure. The salt, sal ammoniac, for example, has a vapour pressure higher than 760 mm Hg and thus sublimes from the solid to the vapour at ambient atmospheric pressures. In order for ice to sublime, however, it is necessary to reduce the pressure to which it is exposed to values less than or equal to its vapour pressure at its particular temperature, e.g. the pressure must be reduced to 1.95 mm Hg, if the ice is at -10C (Fig. 3).
Therefore, consider the situation illustrated in Fig. 4, where flask A
is at a temperature T1 and condenser B is at a temperature T2, both T1and T2 being below the freezing point of ice but T1>T2. It follows then that if P, the overall pressure within the system, is less than VpT1 (the vapour pressure of ice at temperature T1) and more than VpT2 (the vapour pressure of ice at temperature T2), ice will sublime in flask A and condense in B.
Figure 4. A simple freeze-dryer.
In a practical freeze-dryer, T1 will be about -10∞C and T2 will be about -50C. V pT1 will thus be about 1.95 mm Hg and VpT2 will be about 0.029 mm Hg (Fig. 3). “P”, the pressure measured on the vacuum gauge, must therefore be between 1.95 mm Hg (1,950 microns) and 0.029 mm Hg (29 microns): in practice it is usually between 500 and 100 microns, when the freeze dryer is operating properly.
With regard to the net transport of water vapour from A to B an analogy can be drawn with electricity, i.e. where in electricity,
In freeze-drying,
The constant in the “resistance” term in equation.1 describes in part the geometry of the piping system connecting flask A and condenser B and is minimal when this is short and wide. To achieve a maximal rate of freeze-drying, therefore, it is necessary to establish:-
• A maximal vapour pressure difference between the sample and the condenser,
• a minimum pressure of permanent gases, and,
• a minimum value of the piping geometry constant.
Most of these factors are fixed by the design of a particular machine but it is useful for the researcher to have an appreciation of their influence. For example, the first item, considered in conjunction with Fig. 3, suggests that there is no advantage to be gained in using a condenser temperature much below -50C, since below this temperature there is little change in the vapour pressure of ice (since it is asymptotic to zero). A temperature of -50C can be achieved with single-stage refrigeration systems and there is thus little benefit in using expensive two-stage systems to reach a lower condenser temperature.
As ice sublimes from flask A it removes latent heat of sublimation, which keeps the remaining ice cold. The heat removed by sublimation is replaced by heat from the atmosphere, especially the latent heats of condensation and freezing of ice condensing on the outside of the flask. A thermal gradient is thus formed through the layers of ice and the wall of the freeze-drying flask (Fig. 5), and a dynamic equilibrium is established in which the rate of heat input to the system is balanced by the rate of heat loss. At equilibrium, the rate of heat input is the factor limiting the rate of freeze-drying. However, a limit to this rate of input is determined by the point at which the sample melts.
Figure 5. Thermal gradient across a freeze-drying flask and its associated ice layers.
The nature of the system has the following practical ramifications:-
• The greater the area over which the sample is spread, the greater will be the rate of heat input and the faster will be the rate of freeze-drying;
• The sample layer should be as thin as possible since if it is too thick there is a risk of the sample melting on its outermost surface, due to the thermal gradient. (Note: If this should happen, the sample should not be re-frozen as the melted sample, being trapped between the flask wall and the frozen part of the sample, might crack the flask as it expands upon re-freezing.)
• The flask should be made of a material with a high thermal conductivity: thus glass is commonly used. When the freeze-dryer is in operation, there is a flow of heat through the system, as illustrated in Fig. 6.
Figure 6. The heat flow through a freeze dryer in operation.
Atmospheric heat enters the freeze drying flask, via the ice condensing on the outside of the flask. The heat is transferred through the flask and is removed by the subliming water vapour. When this water vapour condenses, in the condenser, the heat is transferred to the refrigerant gas and is ultimately returned to the atmosphere via the radiator of the refrigeration unit.
1.2 Some tips on vacuum
Many people have confused thoughts about vacuums and so a few words on the subject may be useful. A vacuum may be defined as any pressure less than the prevailing ambient pressure. Since vacuums are defined in terms of a pressure differential, clear thinking is easier if one thinks only in terms of pressure, which has a range from zero to “infinity”.
Ambient pressure is usually about one atmosphere, or 760 mm Hg, or about 15 p.s.i. (“p.s.i.” or pounds per square inch is an old measure but one which is easy to visualise. 1 p.s.i. ≈ 6.89 kPa). An absolute vacuum, which is practically unattainable, corresponds to a pressure of zero. The theoretical maximum pressure differential across the walls of a vessel in the atmosphere but “containing” an absolute vacuum is therefore one atmosphere, i.e. 760 mm Hg or about 15 p.s.i. This is not a large differential, as pressures go, and there is clearly no truth in the belief that, “if one sucks hard enough, almost any vessel can be made to collapse!”
How hard can one suck on water?
Everyone is familiar with the process of drinking water from a container by using a straw.
Q: Is there a limit to the length of the straw, i.e. to the height that the water can be sucked up?
A: Yes. In the case of water the limit is about 7 metres, which is the height to which the atmospheric pressure can lift a column of water. The equivalent height of a column of mercury is 760 mm (do this only as a “thought experiment”, though, since mercury is very toxic!)
Figure 7. How far can water be sucked up?
This is why farmers have their water pumps near the bottom of the valley, near the river. The pump can only “suck” the water up a limited distance (about 7 meters vertical height) but it can push it up much further than this.
Q: What limits the water from being sucked up higher than 7 meters? A: The water will boil (i.e. be converted to vapour) when the pressure applied to it becomes less than its vapour pressure at the prevailing temperature.
In engineering terms the point to remember about pressure differentials is that the resultant force is a function of the area over which the differential exists. Consider, for example, the force acting upon the Perspex lid of a typical laboratory freeze dryer. If the lid is 8 inches in diameter (1 inch = 2.54 cm) it will have an area of ca. 50 square inches. At a pressure differential of 15 p.s.i., the force acting on the lid is equivalent to ca. 750 pounds weight (ca. 340 kg): no wonder it
bows inward. If one could get a good enough grip, one could lift the entire machine by its lid once the vacuum was established!
On the other hand, what is a high vacuum and how is it different to a “non -high vacuum”? An atmosphere corresponds to a pressure of 760 mm Hg. A pressure of 1 mm Hg is not really in the high vacuum range but the force applied to the system would be of the ultimate force. High vacuum pumps “split” the last mm of Hg and 0.5 mm Hg (500 microns) requires a high-vac pump, but the forces on the system will increase by only 0.5/760 or 0.07%, a negligible amount!
A generalization can therefore be made: that if a system is structurally strong enough to withstand a moderate vacuum of 1 mm Hg (1000 microns) it will probably withstand any possible high vacuum! (Remember that attaining high vacuums is like splitting hairs!). In practical terms this means that one should not be too nervous of flasks imploding under vacuum. A flask is more likely to break due to thermal stress or mechanical abuse (point impacts) than under vacuum loads per se.
Nevertheless one should be aware that the likelihood of a flask failing, from whatever cause, increases with the size of the flask.
References
-Dennison, C. (2002). A guide to protein isolation . School of Molecular mid Cellular Biosciences, University of Natal . Kluwer Academic Publishers new york, Boston, Dordrecht, London, Moscow .
الاكثر قراءة في عزل البروتين
اخر الاخبار
اخبار العتبة العباسية المقدسة
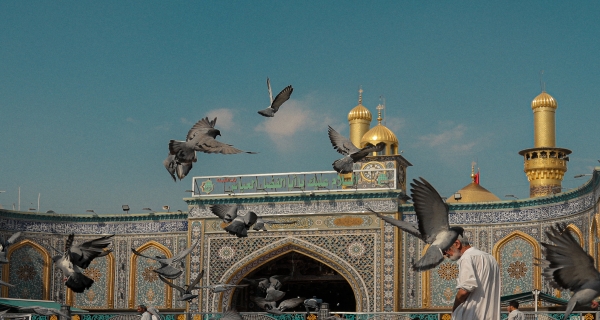
الآخبار الصحية
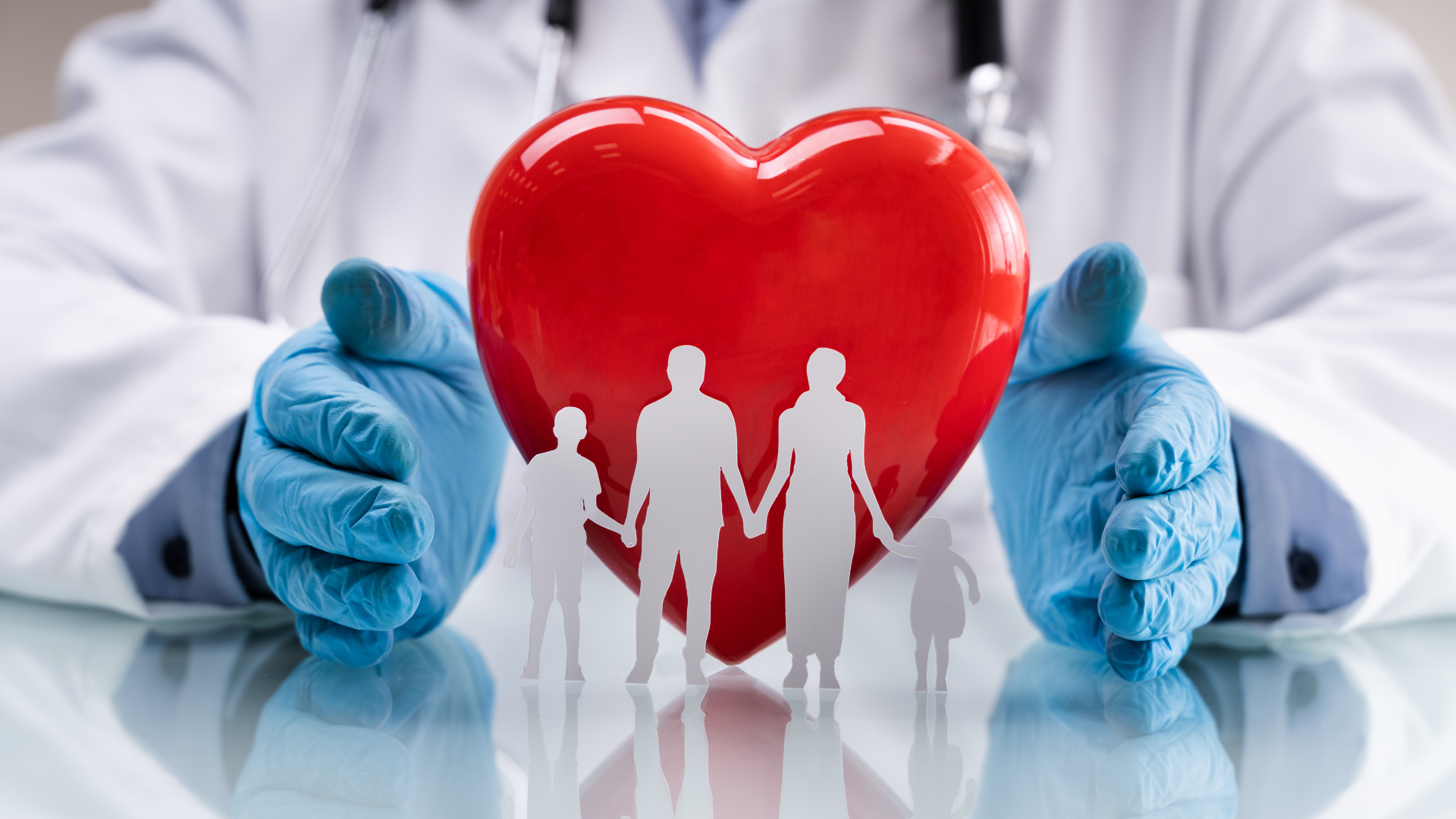