المحاسبة
تطور الفكر المحاسبي
الافصاح والقوائم المالية
الرقابة والنظام المحاسبي
نظرية ومعايير المحاسبة الدولية
نظام التكاليف و التحليل المحاسبي
نظام المعلومات و القرارات الادارية
مواضيع عامة في المحاسبة
مفاهيم ومبادئ المحاسبة
ادارة الاعمال
الادارة
الادارة: المفهوم والاهمية والاهداف والمبادئ
وظائف المدير ومنظمات الاعمال
الادارة وعلاقتها بالعلوم الاخرى
النظريات الادارية والفكر الاداري الحديث
التطور التاريخي والمدارس والمداخل الادارية
وظيفة التخطيط
انواع التخطيط
خطوات التخطيط ومعوقاته
مفهوم التخطيط واهميته
وظيفة التنظيم
العملية التنظيمية والهيكل التنظيمي
مفهوم التنظيم و مبادئه
وظيفة التوجيه
الاتصالات
انواع القيادة و نظرياتها
مفهوم التوجيه واهميته
وظيفة الرقابة
انواع الرقابة
خصائص الرقابة و خطواتها
مفهوم الرقابة و اهميتها
اتخاذ القرارات الادارية لحل المشاكل والتحديات
مواضيع عامة في الادارة
المؤسسات الصغيرة والمتوسطة
ادارة الانتاج
ادارة الانتاج: المفهوم و الاهمية و الاهداف و العمليات
التطور التاريخي والتكنلوجي للانتاج
نظام الانتاج وانواعه وخصائصه
التنبؤ والتخطيط و تحسين الانتاج والعمليات
ترتيب المصنع و التخزين والمناولة والرقابة
الموارد البشرية والامداد والتوريد
المالية والمشتريات والتسويق
قياس تكاليف وكفاءة العمل والاداء والانتاج
مواضيع عامة في ادارة الانتاج
ادارة الجودة
الجودة الشاملة: المفهوم و الاهمية و الاهداف و المبادئ
نظام الايزو ومعايير الجودة
ابعاد الجودة و متطلباتها
التطور التاريخي للجودة و مداخلها
الخدمة والتحسين المستمر للجودة
خطوات ومراحل تطبيق الجودة الشاملة
التميز التنافسي و عناصر الجودة
مواضيع عامة في ادارة الجودة
الادارة الاستراتيجية
الادارة الاستراتيجية: المفهوم و الاهمية و الاهداف والمبادئ
اساليب التخطيط الاستراتيجي ومراحله
التطور التاريخي للادارة الاستراتيجية
النظريات و الانظمة و القرارات و العمليات
تحليل البيئة و الرقابة و القياس
الصياغة و التطبيق و التنفيذ والمستويات
مواضيع عامة في الادارة الاستراتيجية
ادارة التسويق
ادارة التسويق : المفهوم و الاهمية و الاهداف و الانواع
استراتيجية التسويق والمزيج التسويقي
البيئة التسويقية وبحوث التسويق
المستهلك والخدمة والمؤسسات الخدمية
الاسواق و خصائص التسويق و انظمته
مواضيع عامة في ادارة التسويق
ادارة الموارد البشرية
ادارة الموارد البشرية : المفهوم و الاهمية و الاهداف و المبادئ
التطور التاريخي لادارة الموارد البشرية
استراتيجية ادارة الموارد البشرية
الوظائف والتعيينات
الحوافز والاجور
التدريب و التنمية
السياسات و التخطيط
التحديات والعولمة ونظام المعلومات
مواضيع عامة في ادارة الموارد البشرية
نظم المعلومات
علوم مالية و مصرفية
المالية العامة
الموازنات المالية
النفقات العامة
الايرادات العامة
مفهوم المالية
التدقيق والرقابة المالية
السياسات و الاسواق المالية
الادارة المالية والتحليل المالي
المؤسسات المالية والمصرفية وادارتها
الاقتصاد
مفهوم ونشأت وعلاقة علم الاقتصاد بالعلوم الاخرى
السياسة الاقتصادية والمالية والنقدية
التحليل الأقتصادي و النظريات
التكتلات والنمو والتنمية الأقتصادية
الاستثمار ودراسة الجدوى الأقتصادية
ألانظمة الاقتصادية
مواضيع عامة في علم الاقتصاد
الأحصاء
تطور علم الاحصاء و علاقته بالعلوم الاخرى
مفهوم واهمية علم الاحصاء
البيانات الأحصائية
موازنة خط التجميع Balancing The Assembly Line
المؤلف:
د . عبد الكريم محسن د . صباح مجيد النجار
المصدر:
ادارة الانتاج والعمليات
الجزء والصفحة:
ص341-344
16-2-2021
4249
1 - 2 - 4 - 8 موازنة خط التجميع Balancing The Assembly Line
إن الصفة المميزة بين الترتيب على اساس العملية و الترتيب على أساس المنتوج تتمثل في نوع تدفق العمل (Work Flow) ، فهو متغير في الترتيب على أساس العملية ويصعب التنبؤ به ، على حين يسهل التنبؤ بتدفق العمل في الترتيب على أساس المنتوج لأنه دالة لمراحل التجميع أو الإنتاج المطلوبة لمنتوج ما . لذلك فإن ترتيب المواقع النسبية للنشاطات والتكنولوجيا المستخدمة لا تشكل تحدياً كبيراً لمدير العمليات مقارنة بالترتيب على أساس العملية.
قبل الدخول في تفاصيل موازنة خط التجميع لابد من تعريف المصطلحات الاتية :
• خط التجميع Assembly Line : مجموعة من محطات العمل مسؤولة عن تجميع منتوج معين وفق مراحل محددة بحيث تكون مخرجات كل محطة عمل مدخلات للمحطة التالية مباشرة ، وتنتقل المواد بين المحطات إما يدوياً أو باستخدام الأحزمة الناقلة (Conveyors) أو انسيابياً بفعل الجاذبية الأرضية .
• محطة العمل ( ws) Work Station : مجموعة من العمال أو الآلات أو العمال والآلات مكلفة بإنجاز نشاط أو مجموعة من النشاطات .
• النشاط (Task): مجموعة من الفعاليات (Actions) يمكن تمييزها عن الفعاليات الأخرى وتُنجز في محطة عمل.
• محتوى العمل (Job Content (JC : هو مجموع الأوقات اللازمة لإنجاز جميع الأنشطة المتعلقة بتجميع وحدة واحدة من المنتوج .
• وقت دورة الإنتاج النظرية (CT) Theoretical Cycle Time : وهي حاصل قسمة الوقت المتاح للإنتاج باليوم على الطلب اليومي، وتُحسب بالقاعدة الاتية :
إذ إن: PT = الوقت المتاح للإنتاج باليوم Day /Time Production
D= الطلب اليومي (Day / Demand)
• العدد النظري الأدنى لمحطات العمل WSt
Theoretical Minimum Number of Work Stations.
هو عبارة عن حاصل قسمة محتوى العمل (JC) على دورة الإنتاج النظرية (Ct) ويحسب بالقاعدة الآتية :
• وقت دورة الإنتاج الفعلية (Ca) Actual Cycle Time
وهي المدة الزمنية بين خروج وحدة تامة الصنع وأخرى وتحسب على أساس محطة العمل التي تحصل على أكبر مجموع من الأوقات المخصصة للأنشطة من بين جميع محطات العمل على خط التجميع وبذلك فأن وقت دورة الانتاج الفعلية هي اقصى وقت يمكن أن يقضيه المنتوج او احد اجزائه في كل محطة من محطات عمل خط التجميع.
• الكفاءة Efficiency ( E ) : وهي النسبة المئوية بين محتوى العمل وحاصل ضرب عدد المحطات النظري (WSt) في وقت دورة الإنتاج، وتحسب الكفاءة بالقاعدة الاتية:
ويُستعاض عن العدد النظري لمحطات العمل (WSt) بالعدد الفعلي لمحطات العمل في القاعدة (8-3) اعلاه عندما يضطر مدير العمليات في بعض الأحيان إلى تجاوز العدد النظري لتلك المحطات إما بالزيادة أو النقصان للوصول إلى موازنة كفوءة لخط التجميع ويسمى العدد الجديد لمحطات العمل بالعدد الفعلي لمحطات العمل (WSa) لذلك يحل (WSa) محل (WSt) في القاعدة (8-3)عند حساب الكفاءة.. عند ذلك تصبح القاعدة (8-3) كالآتي:
كما يمكن حساب الكفاءة أيضا عن طريق النسبة المئوية بين العدد النظري لمحطات العمل (WSt) والعدد الفعلي لمحطات العمل (WSa) أي بالقاعدة (8-5) الآتية :
• نسبة الوقت الضائع B( %) Balance Time : وتحسب بالقاعدة (8-6)
B = 100 % - E ….. ( 8-6)
• الوقت العاطل أو الضائع ( I) Idle Time : وهو المجموع غير المستغل من وقت الإنتاج في جميع المحطات ويُحسب بالقاعدة الأتية:
I = (WSa X Ct) – JC ……… (8-7)
إن الهدف من موازنة خط التجميع هو القضاء على ظاهرتي الإختناق (Bottleneck) والوقت الضائع (Idle Time) للحصول على الإنتاج المطلوب. وتحدث ظاهرة الوقت الضائع عندما يكون الوقت المخصص لإحدى المحطات (محطة 2) أقل من الوقت المخصص للمحطة السابقة (محطة 1) مباشرة إذ يكون الوقت الضائع في المحطة (2). على حين تحدث ظاهرة الإختناق عندما يكون الوقت المخصص لإحدى المحطات (محطة 1) اقل من الوقت المخصص للمحطة التابعة (محطة 2) مباشرة لذلك يتراكم خزين من المواد تحت التشغيل (WIP) أمام المحطة (2) في خط الإنتاج عند حدوث هذه الظاهرة، فيكون الاختناق في المحطة (2).
ان الظاهرين السابقتين يمكن القضاء عليهما عن طريق توزيع النشاطات على المحطات بشكل متساوٍ قدر الإمكان، ومن المعروف أن خط الإنتاج المتوازن يحقق نسب إستغلال عالية للعمال ولتقنيات الإنتاج ويحقق أيضاً عدالة في توزيع عبء العمل بين العمال على خط التجميع.
والشكل (8-5) (أ) يوضح خط انتاج يتضمن وجود وقت ضائع ، اما الجزء (ب) فإنه يمثل حالة الاختناق
إن موازنة خط التجميع يمكن أن تنطلق من نقطتين:
(أ) إما إيجاد العدد النظري الأدنى لمحطات العمل لدورة إنتاج معروفة، أو (ب) إيجاد دورة الإنتاج الأصغرية لعدد معروف من محطات العمل. فإذا كان مدير العمليات أمام حالة (أ) فإن المشكلة هي مشكلة ترتيب (Layout)، وإذا كانت الحالة المطروحة هي (ب) فإن المشكلة هي جدولة أعمال (Scheduling). وتتم معالجة الحالتين أ و ب في آن واحد ذلك لأن من يقوم بالترتيب لا بد له من القيام بتوزيع النشاطات على محطات العمل.
وبهدف إعداد ترتيب على أساس المنتوج ينبغي على مدير العمليات معرفة الأدوات وأساليب العمل المستخدمة والوقت اللازم لإنجاز كل نشاط وعلاقة التتابع بين النشاطات (Precedence Relationship). والمثال الاتي سيوضح كيفية إعداد ترتيب الخط تجميع وموازنته.
الاكثر قراءة في ترتيب المصنع و التخزين والمناولة والرقابة
اخر الاخبار
اخبار العتبة العباسية المقدسة
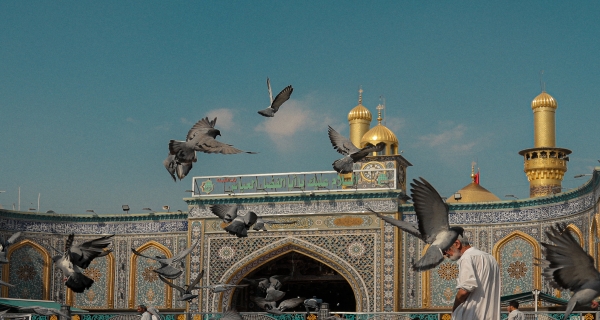
الآخبار الصحية
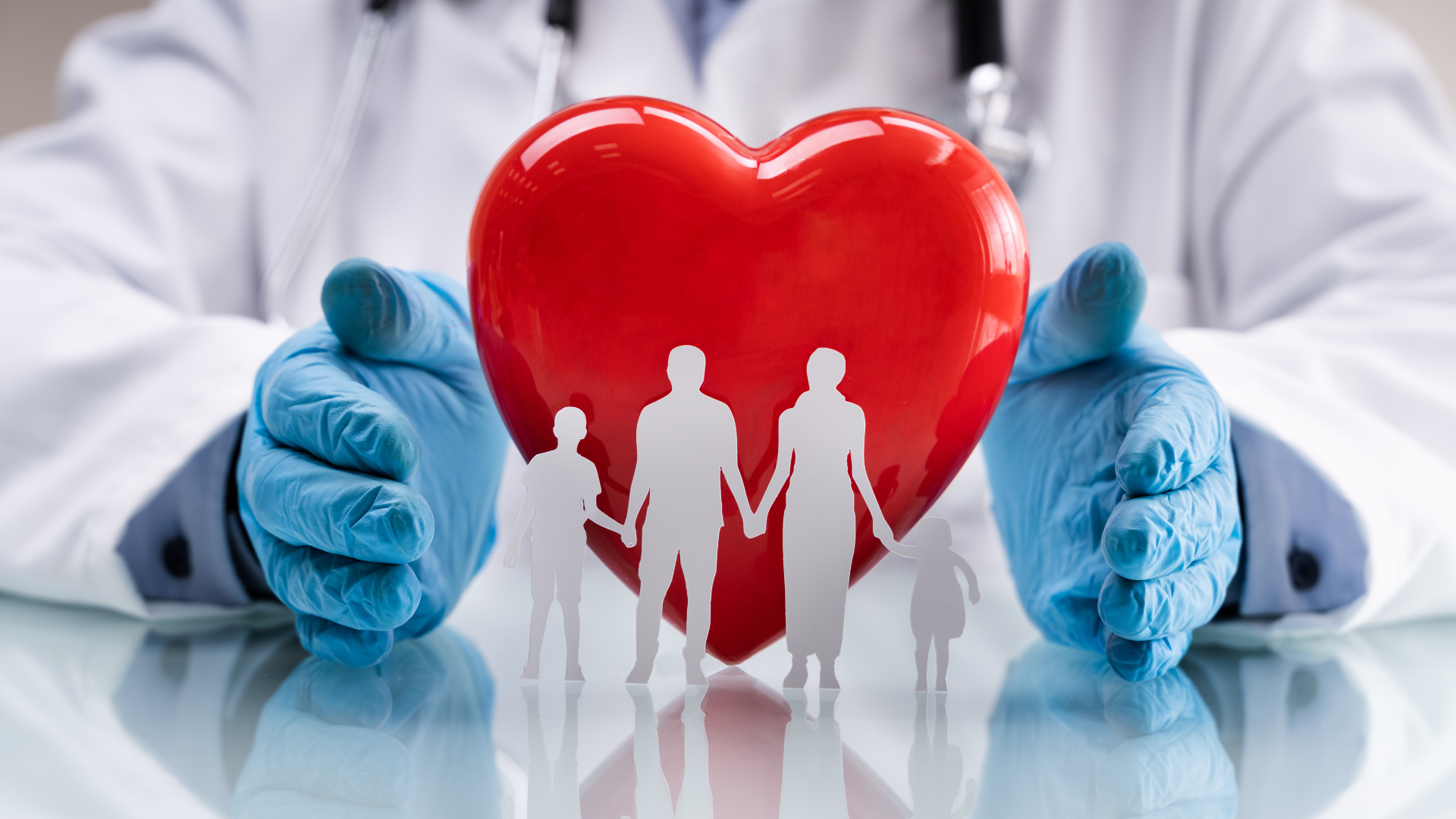